Supplies for Textile Printing
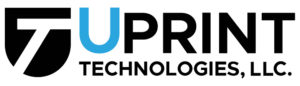
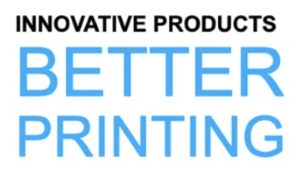

Supplies for Textile Printing
UPrint Technologies offer supplies for textile printing, both rotary screens and photo-emulsions, to meet the quality requirements of your customers.
Rotary Screens for Textile Printing
For any textile printing job, UPrint Technologies offers the right rotary screens for you. Enabling your customer, to print the most challenging design at the highest quality.
With our unique technology we reach bigger hole size and shape, while keeping high mesh. Thanks to the high mesh and bigger open area, UPrint Technologies screens exhibit excellent printing performance.
Photo-emulsions
UPrint Technologies provides different types of highly efficient photo-emulsions. Due to the unique formulation, our photo-emulsions will provide sharp and crisp design details, which will reflect in the printing results. Our photo-emulsions are available for both exposing as well as engraving technologies.
Specification Sheet
Mesh | Thickness (um) | Open Area (%) | Hole Size (um) | Finest Line | |
Eco Screen | 40 | 150 | 30 | 318 | 0.63 |
60 | 120 | 20 | 161 | 0.42 | |
80 | 115 | 18 | 131 | 0.31 | |
105 | 115 | 16 | 94 | 0.24 | |
125 | 105 | 15 | 79 | 0.21 | |
125V | 105 | 15 | 79 | 0.21 | |
155V | 105 | 13 | 60 | 0.16 | |
Uni Screen | 125V | 110 | 19 | 86 | 0.21 |
135V | 120 | 23 | 88 | 0.19 | |
165V | 115 | 19 | 67 | 0.15 | |
195V | 115 | 19 | 55 | 0.13 |
Repeat in mm (inch) : 640 (25″) – 688 (27″) – 725 (28″) – 914 (36″) – 1018 (40″)
Screen Cut length in mm : 1980 – 2080 – 3050 – 3500
WEKO NEO
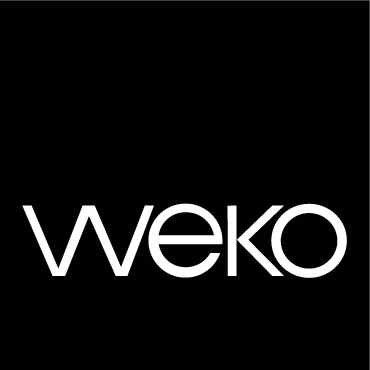
TEXTILE REVOLUTION WITH WEKO | NEO

WEKO | NEO
Textile revolution with WEKO | NEO is here. Since the world-wide textile production is suffering from cost pressure and the desire to reduce consumption of water, energy and chemicals. Therefore, the advanced WEKO | NEO technology combines a more sustainable process with cost saving production.
A newly developed innovation for the textile industry to revolutionize the wet-on-wet and wet-on-dry finishing process. For instance, immense water, energy and chemical savings will help you to a sustainable production process. What’s more, the WEKO | NEO is used for a large variety of finishing applications in the Textile World and can be also used for Yarn dying. In addition, WEKO has partnered with Chemical Manufacturers to find excellent savings and product effects in the DENIM Manufacturing.
The WEKO | NEO technology in brief – Single or both sides fluid application
The specially designed WEKO | NEO system and the new processing is adaptable to any existing or new stenter frame, coating or Pad-Steam line or on any section of a slasher or loop dyeing range. One system fits it all spending the given savings in resources and costs.
Preferred Supplier Status
Brands and retailers are massive looking for new sustainable textile processing. Be the most liked brand supplier!

WEKO | NEO
Your Benefits
- Uniform, precise and contactless minimum application
- Single-sided, double-sided or double-sided different application
- Dye bath / chemical bath remains clean
- no tailing
- No center-side variation
- Low pick-up of only 12-35
- up to 80% less drying energy
- up to 80% less fresh and waste water consumption
- up to 60% less chemical consumption
- Easy installation also on existing machines
- Easy operation via touch screen