Innovative Doctor Blades
MOVING FORWARD, TOGETHER
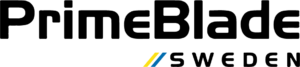
Innovative Doctor Blades by PrimeBlade Sweden
Increase of printing speeds, more colors as well as demand of finer details are today’s challenges in flexographic and gravureprinting. Doctor blades, for example, are used in the most sensitive area of the printing process. Thus there is where the end result is determined. Innovative Doctor Blades by PrimeBlade is how we define solutions for better printing.
We want to make it easier
It is the back bone of PrimeBlade Sweden to make the printing process easier. To create a worry-free print production, with high uptime, reduction of waste as well as keeping production teams happy. That journey starts with finding the right doctor blade for your jobs. Together, we will go over your press operation set-up, length of job, anilox, and also specific inks used. After all, it is necessary to consider the application, i.e. the environment that the material will experience. For that purpose, we have different solutions for any application, in flexo-, gravure, as well as offset printing.
INNOVATIVE PRODUCTS. BETTER PRINTING
A highly innovative technology in doctor blades: Nano. Following a precision technology treatment of the highest quality steel, with the objective to reduce the wear, combined with an increase of the lifetime of the doctor blade and anilox. This special treatment also reduces the environmental impact, which is the objective of many brand owners. Therefore, when choosing PrimeBlade doctor blades, you also choose for a circular solution.

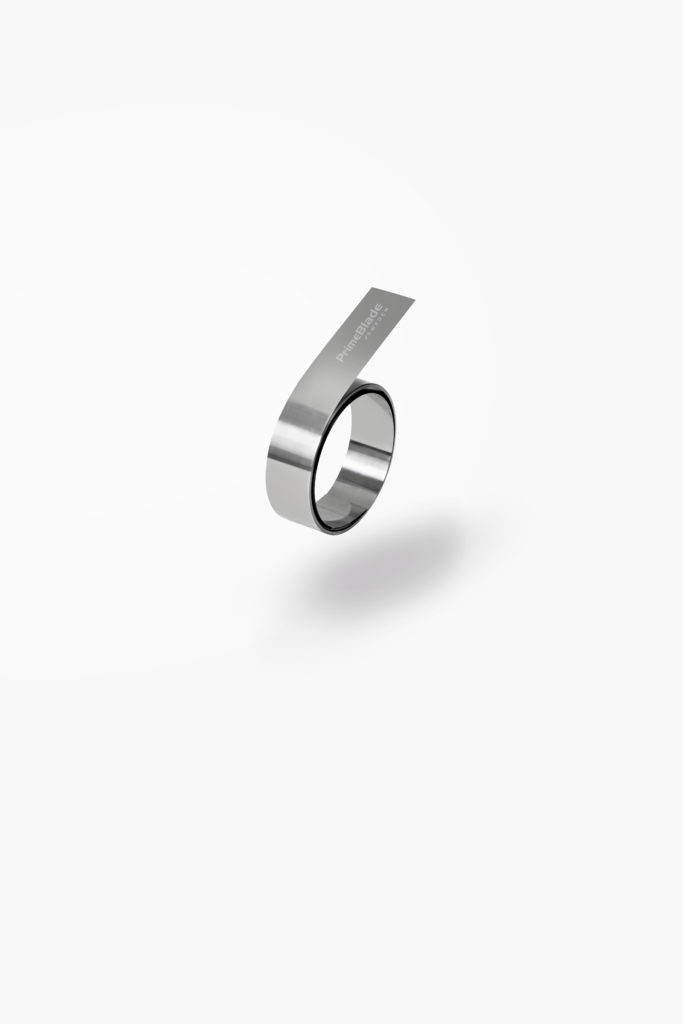
Innovation is the key to support the printing process. The state of the art, world-class 900 Nano series products will improve the printing quality. This series is a unique range of doctor blades with enhanced properties. A special patented treatment, inducing changes in the steel, provides reduced wear and thus longer lifetime, as well as improved surface quality.
Complete program
PrimeBlade Sweden completes the supply program with high quality Prime | Seals.
Choosing a world-class supplier
When choosing PrimeBlade high quality doctor blades, you also choose for reliable and the best in class support, such as education, consultation and technical support.
Viscosity sensor by Rheonics
PRINT QUALITY IS ALL ABOUT VISCOSITY MANAGEMENT
MEET THE NEXT GENERATION VISCOSITY CONTROL SENSOR
RPS InkSight
A RPS InkSight system maintains the highest printing quality standards through tight and accurate viscosity control.
Printing Quality. It is all about viscosity
Leading manufacturers of printing machines equip the current generation of equipment with highly sophisticated quality control and automation systems. After all, achieving the best results from your printing equipment requires the control of multiple parameters and thus provides you the best return on investment. One of these parameters that influences your print quality output is viscosity. However, in many press operations this viscosity is determined manually and with low precision, even today.
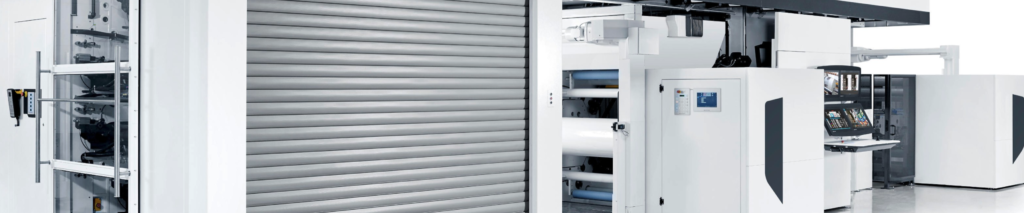
Nevertheless, viscosity is a very important parameter in the final quality of the printed matter. Therefore, it requires close attention given:
- if the viscosity is incorrect, the flow behavior and ink layer thickness will vary, and thus in its turn leading to deterioration of print quality
- poorly adjusted ink viscosity may cause excessive ink consumption and thus unnecessarily high costs
- viscosity automation and predictive tracking control results in waste reduction and efficiency improvements.
Sensors as a solution
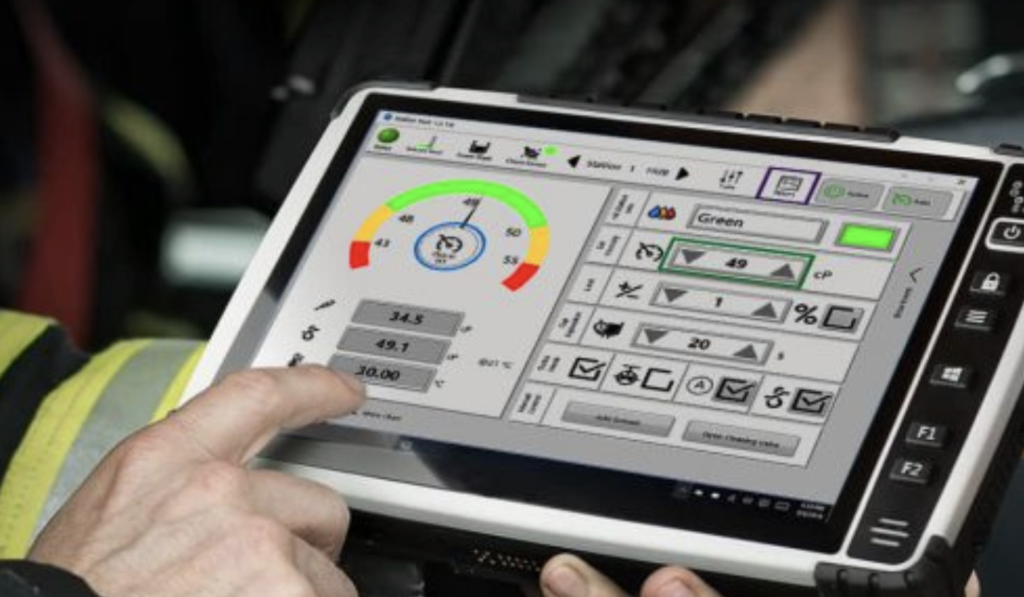
Can the aforementioned goals be achieved? Yes they can. In fact, new technologies in other industries have been successfully transferred to benefit the printing industry. These accurate viscosity measuring sensor enables to determine the viscosity values online and real time. It goes without saying, that these online values attained from this sensor must provide the press operator the confidence that color control and press adjustment systems are reliable. Furthermore, the sensor needs to provide dynamic control of viscosity. Today, there is a solution that enables previously unattainable narrow viscosity limits. Therefore resulting that the print quality is maintained from start-to-finish, even in the longest print runs.
Print quality matters
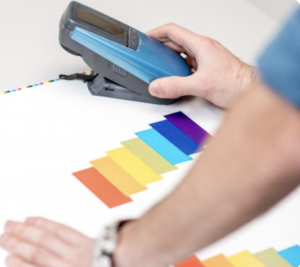
In a highly competitive industry with often tight margins, each job rejected by a customer for unacceptable print quality can be a major blow to both the reputation and the profit of the operator. Thus, the main purpose of viscosity control is to maintain print quality from start to finish of job, no matter the complexity or the run length.
The second goal of viscosity measurement is to improve efficiency, which already starts with setting up the job. Therefore, being able to nail the proper ink viscosity for all print stations without cut-and-dry tinkering means fast job change, will improve the utilization of your print machine capacity.
Achieving the aforementioned goals require a system:
- an accurate and repeatable sensor, that can provide the viscosity resolution necessary for producing accurate and consistent color.
- and also an automatic control system that continually and smoothly adjusts the ink viscosity, considering variables like temperature and rate of evaporation of solvents.
Rheonics RPS InSight
AN AWARD WINNING TECHNOLOGY
2021 FTA Technical Innovation Award
“InkSight fundamentally changes the nature of the flexo printing process, from initial job setup all the way to jobs that, once delivered, secure a clear path to repeat business… It can produce a change in the very culture of the flexo industry by adding job-length consistency, accuracy and efficiency.“
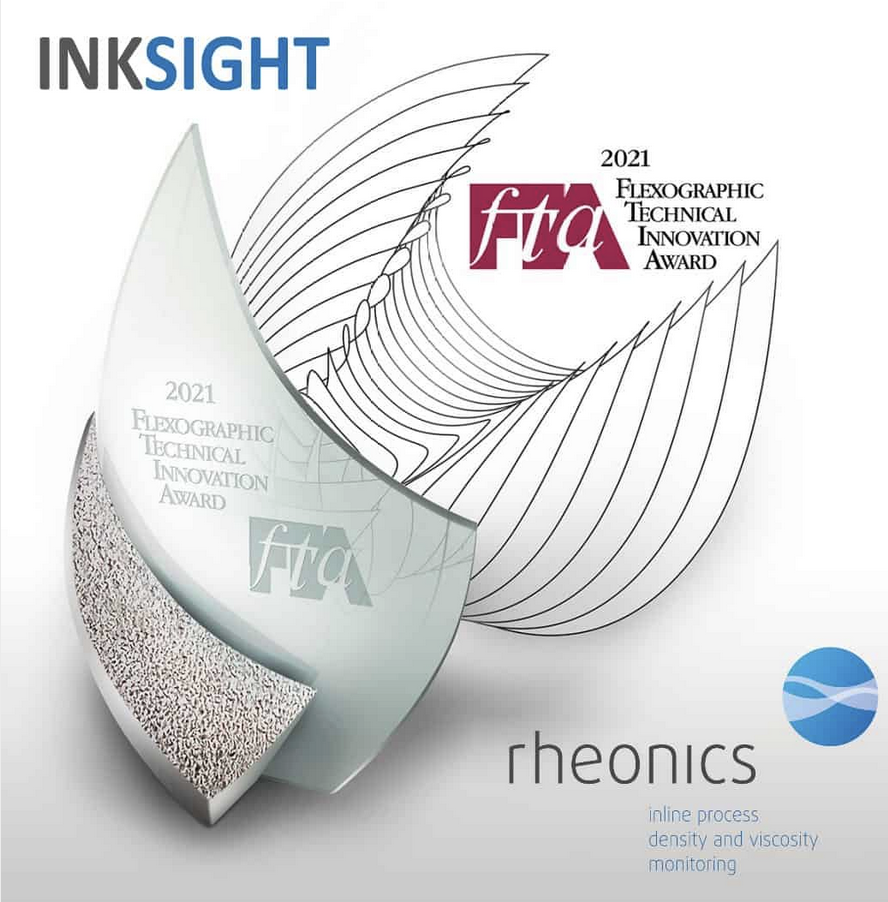
2021 Gravure Awards for Sustainable Packaging by ERA
“Printers can achieve unmatched color accuracy and quality with the InkSight system and ColorLock™ software –which is designed in collaboration with printers, for printers. Viscosity automation and predictive tracking control with InkSight reduces waste and materials consumption, as it increases efficiency and improves quality.“
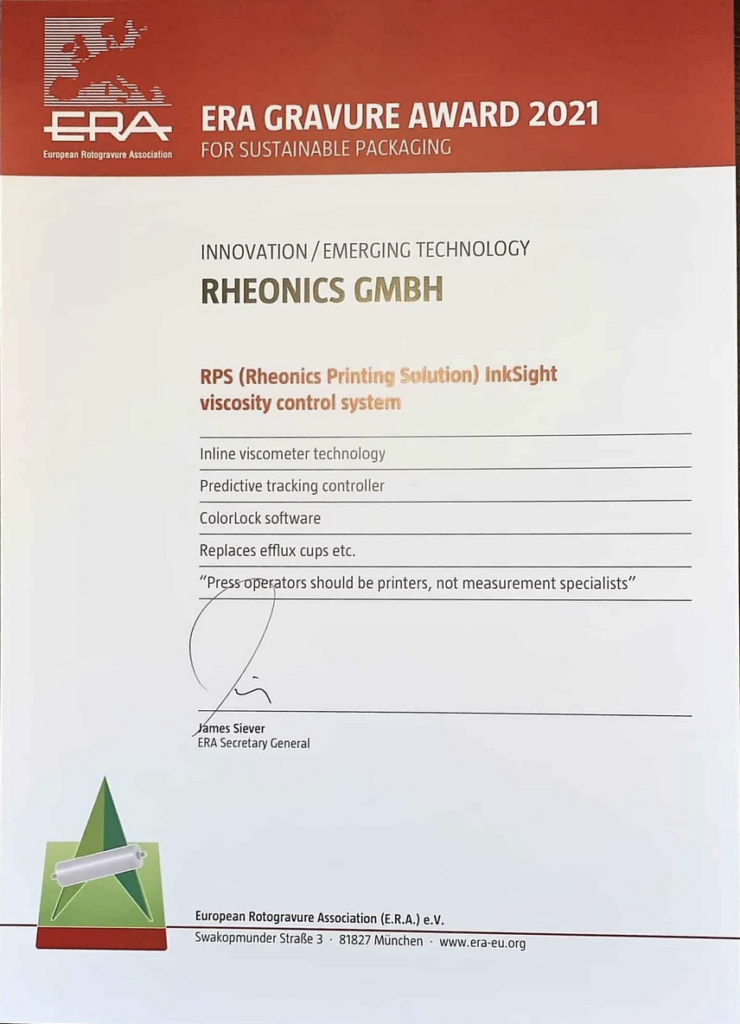
Rheonics RPS InkSight

Meet the revolutionary Rheonics RPS InkSight. This compact symmetric torsional resonator executes microscopic high speed twisting vibrations, therefore not changing the ink behavior in itself. This robust technology is insensitive to both contamination by ink residues and the influence of mechanical vibrations of the printing machine.
This sensor offers high accuracy and reproducibility, and thus making this state of the art technology particular suitable for high-accuracy, reproducible job-to-job matching. The resonator is completely balanced, therefore the accuracy is immune to its mechanical environment.
Furthermore, a Rheonics sensor offers high accuracy and reproducibility, making this state of the art technology particular suitable for high-accuracy, reproducible job-to-job matching. Finaly, the resonator is completely balanced, therefore the accuracy is immune to its mechanical environment.
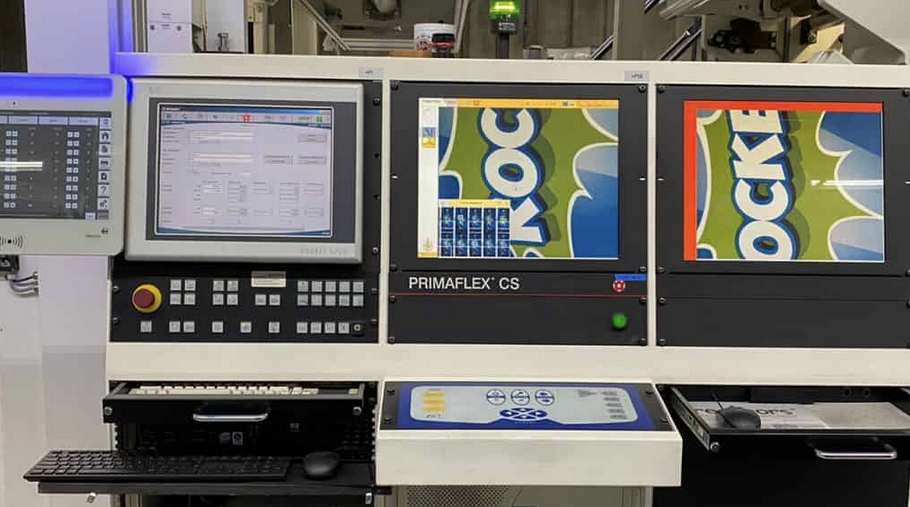
The systems includes a user friendly touchscreen and operates the intuitive user interface of the viscosity control software.
Installation
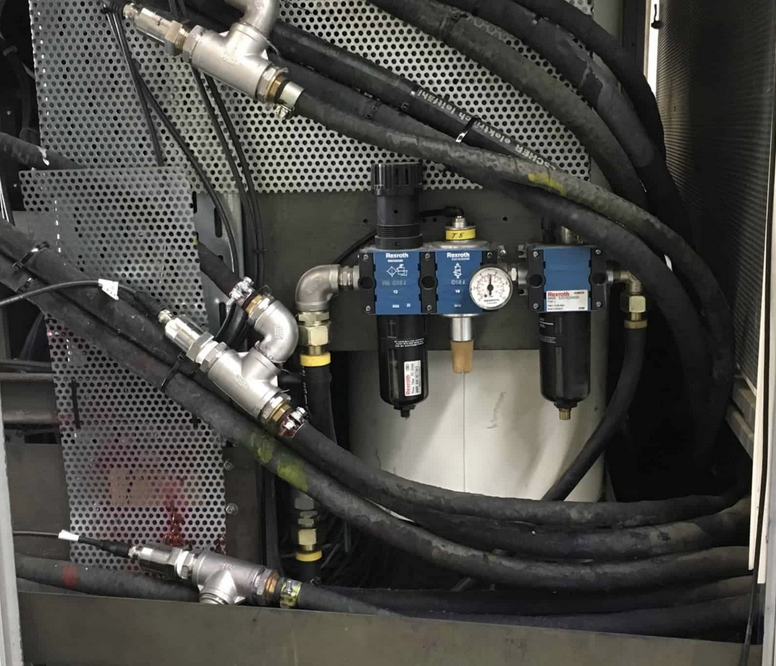
A Rheonics sensor is mounted in a connector with an inlet and outlet opening and installed in the supply line between the ink pump and the doctor chamber. Influences such as machine vibration or pressure pulsations from the diaphragm pump have no effect on sensor operation and reliability of the measurement accuracy.
We connect our sensor via industrial grade cables to their electronic units, which electronics communicate with an industrial grade computer. This computer controls the valve island, to enable valves to automatically dose solvents.
Maintenance
Most importantly, our sensor solution is maintenance free. Your sensors are washed in solvent with each cleaning cycle of the lines and the doctor chamber.
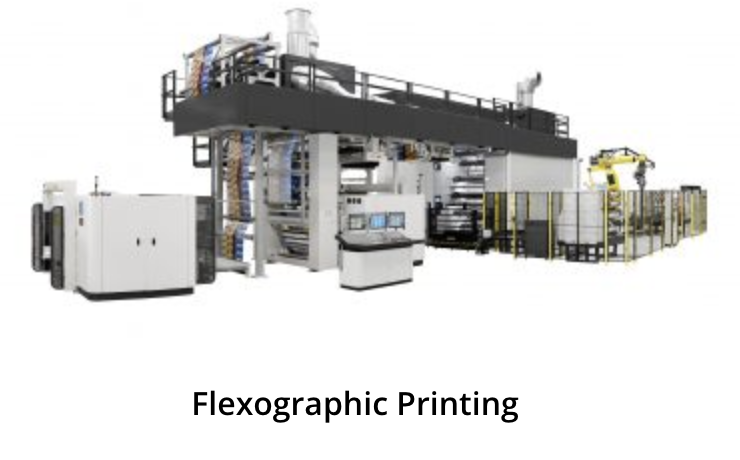
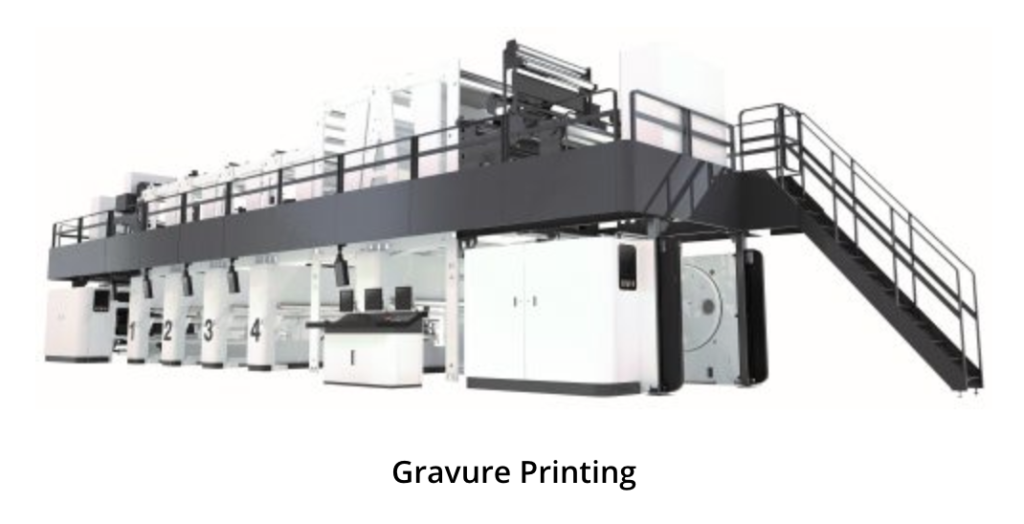
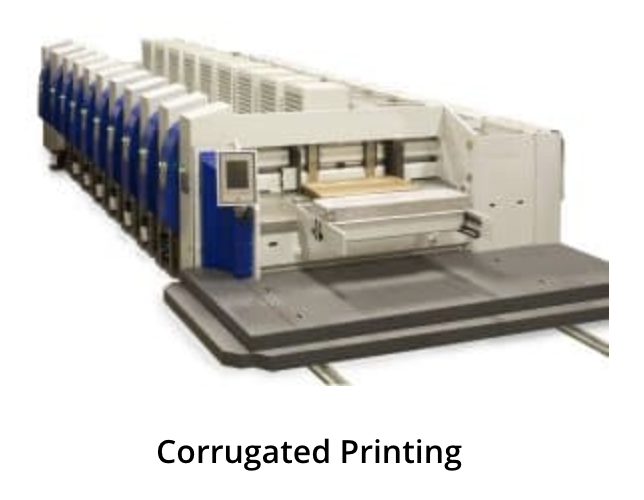
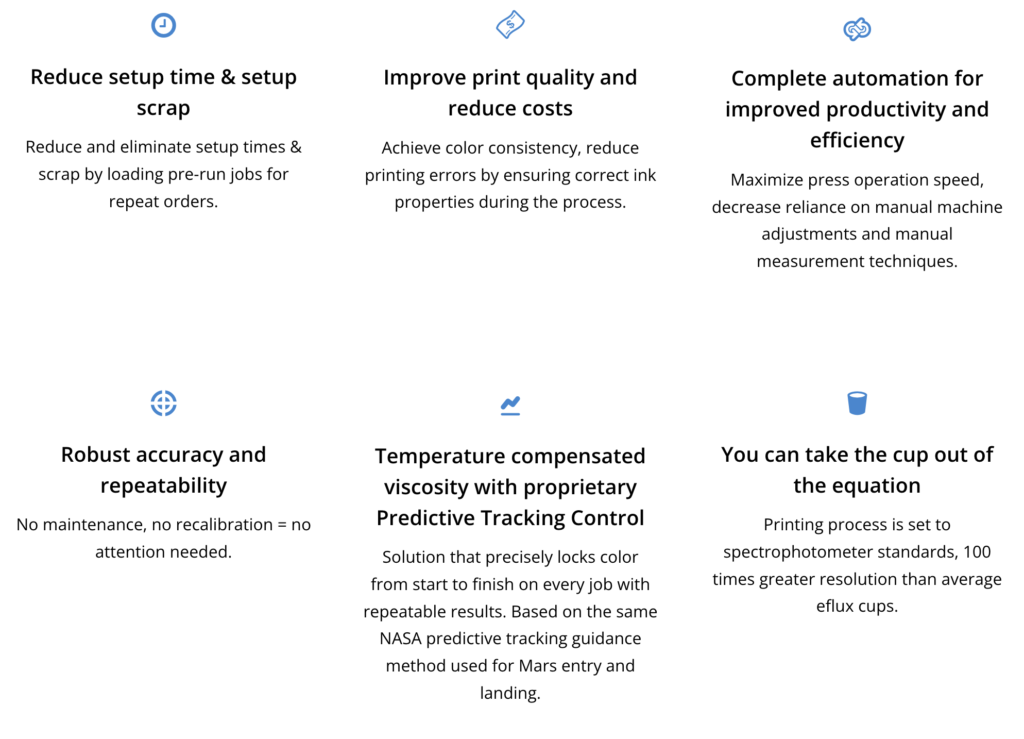