How does viscosity monitoring contribute to better print quality?
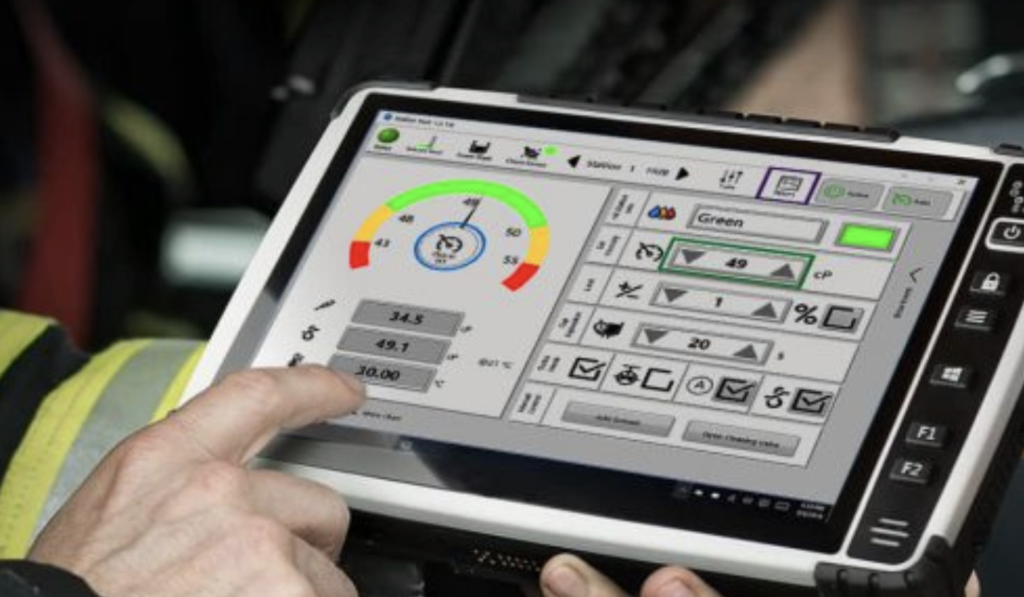
The importance of ink viscosity monitoring in flexo printing
Viscosity is the single most important variable in flexo printing that has a big impact on your print quality output. Monitoring of viscosity during the flexo printing process involves measuring and controlling the consistency or thickness of the ink.
- Consistency: viscosity monitoring helps maintain consistent ink viscosity throughout the printing process. This ensures that the ink flows evenly and consistently onto the substrate.
- Cost savings: you will reduce ink, and substrate waste, as well as downtime.
- Improved print quality: with ink viscosity monitoring you prevent common print defects such as dot gain, color shift, and poor ink transfer.
- Increased productivity: you will reduce the frequency of ink changes and downtime associated with adjusting ink viscosity.
- Improved ink management: by monitoring viscosity, you can better manage your ink inventory by using the ink efficiently. This can lead to a more sustainable and cost-effective printing operation.
What options are available for ink monitoring?
To monitor viscosity, you have different options, such as a viscometer or a rheometer to measure the ink’s viscosity at different stages. You can do this manually or automatically. Automatic viscosity monitoring systems can continuously measure viscosity. And what is more, you can adjust ink flow to maintain consistent viscosity levels throughout the printing process.
What results can you expect when not monitoring properly?
If viscosity is not monitored in flexo printing, you may expect several issues. These issues can negatively impact the printing process and the quality of the printed products, including
- Inconsistent print quality: ink viscosity affects the ink’s flow and transfer properties. Therefore it can lead to uneven ink coverage and color density, resulting in poor print quality;
- Dot gain and color shift: inconsistent ink viscosity can cause dot gain. In that case the dot in the print becomes larger than intended. The color shift, in its turn, is when the printed color deviates from the desired color. These issues can make the final product appear blurry, fuzzy, or distorted;
- Ink waste: inconsistent ink viscosity can cause to discard ink batches that are not suitable for printing. This results in ink waste and increased production costs;
- Downtime and reduced productivity: frequent adjustments to ink viscosity can result in downtime. This will cause delays and reduction in productivity;
- Inefficient use of ink: inconsistent viscosity can result in the ink being used inefficiently, and thus resulting in increased ink consumption and additional costs
Why would you choose automated viscosity monitoring over manual?
There are several reasons why you would prefer automated viscosity monitoring over manual viscosity monitoring
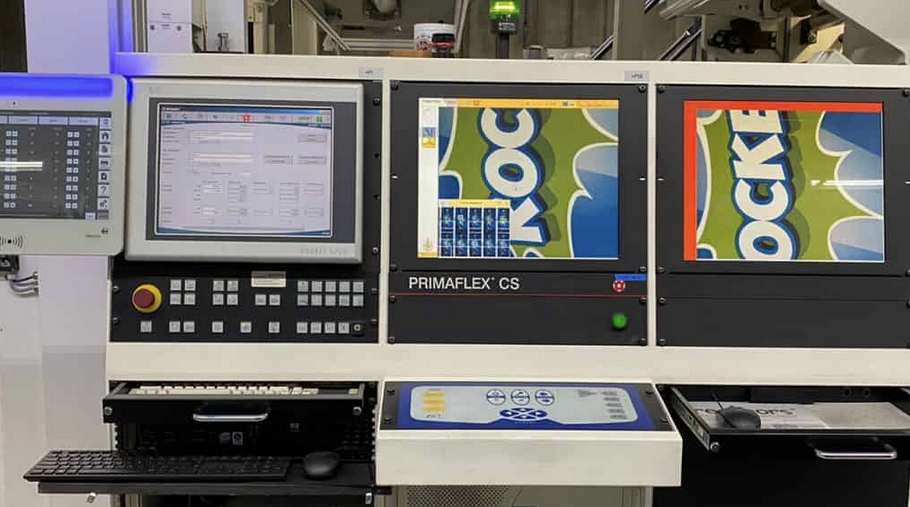
- Increased accuracy: automated viscosity monitoring systems use advanced sensors and software to measure viscosity accurately and consistently. This will result in more precise viscosity readings;
- Time-saving: continuously monitoring viscosity reduces the manual checks and adjustments. Therefore, it saves time and increases productivity;
- Real time adjustments: automated viscosity monitoring systems provide real time adjustments to ink viscosity. That will ensure that the ink remains within optimal range for printing, without the need for manual intervention;
- Cost-effective: the reduction of ink waste, minimizing down-time, and increase of productivity combined, results in cost savings and a more efficient printing process;
- Quality control: automated viscosity monitoring systems will maintain consistent ink viscosity throughout the printing process. Therefore, the print quality remains high and uniform.
Overall, automated viscosity monitoring is a more efficient, accurate, and cost effective way to monitor and control ink viscosity. That is why it is the preferred choice for many printing operations.
How does Rheonics differ from other viscosity monitoring systems?
A Rheonics viscosity monitoring sensor is a compact symmetric torsional resonator. This solution executes at microscopic high speed twisting vibrations. Therefore it does not change the ink behavior in itself. This robust technology is insensitive to both contamination by ink residues and the influence of mechanical vibrations of the printing machine.
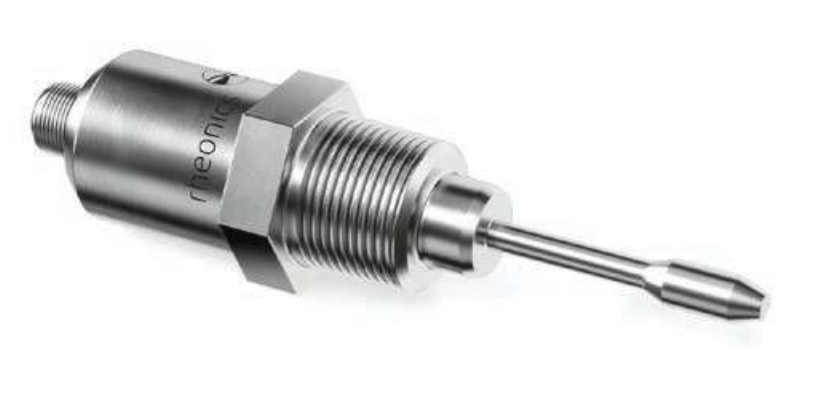
The Rheonics SRV offers high accuracy and reproducibility. The resonator is completely balanced, therefore the accuracy is immune to its mechanical environment. The system comes calibrated and does not need calibration during its lifetime. Furthermore, the Rheonics SRV provides constant viscosity monitoring and real time read out every second. This will keep your viscosity within a very tight range.