Our approach to better printing
MAKE YOUR PRINTING BETTER
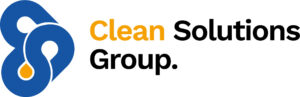

A clean anilox will print better.
Each printing application requires its own cleaning strategy. Therefore, UPrint Technologies puts pride in finding the right cleaning agents for your application. Thus proudly offering Flexoclean solutions.
Anilox…. the heart of your flexo press
When you choose an anilox for your job, you base your decision on getting a continuous, precise and constant ink delivery to your flexo plate. However, during utilization of the anilox it is unavoidable that dry ink will build up in the cells. Thus a balanced anilox cleaning strategy will contribute to your ink delivery expectations. That is why, we believe that a clean anilox will print better.
How do we support you?
UPrint Technologies has a systematic approach in supporting you. That is how we will find your anilox cleaning strategy. Our approach consists of four steps: analyzing, proposing, executing and evaluating.
Analyzing your cleaning needs
Your journey starts with our analysis. This analysis is based upon 25 years of knowledge and specially developed analyzing tools. Your application is tested in our laboratory. The final result is a tailor made concept to support your cleaning requirements.
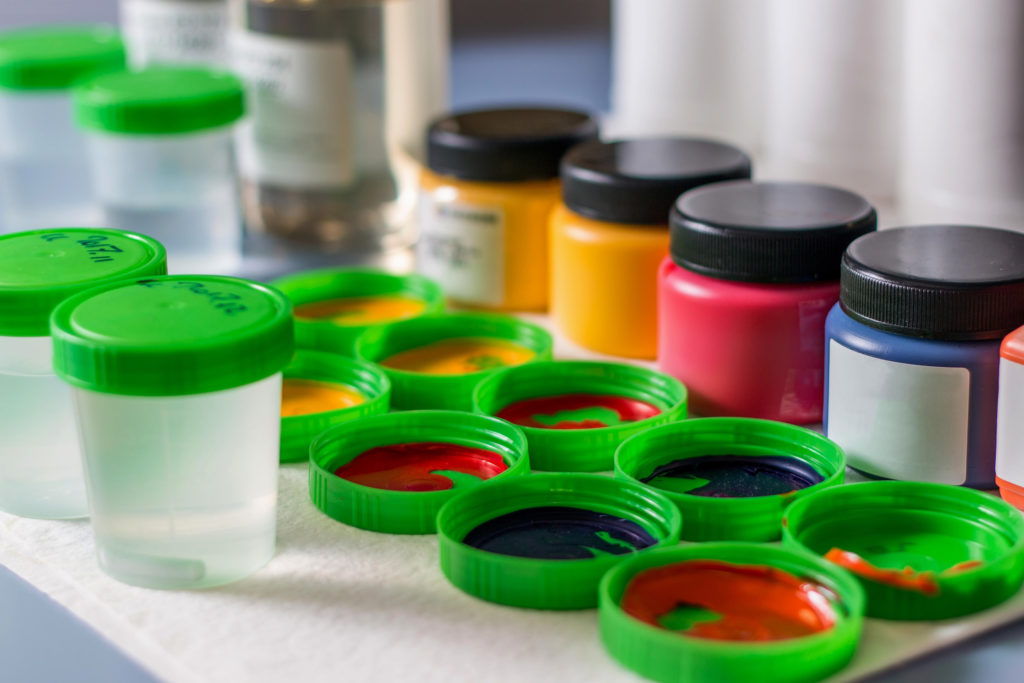
Proposing a balanced cleaning concept
The following step you will receive our concept for daily and periodic cleaning of
- anilox rolls
- flexo plate (for example photopolymer or UP-Flex Plate)
- screen cleaning (for example LABELMesh)
- equipment and spare parts cleaning
Evaluating your cleaning results
Once you have established more experience benefiting from our cleaning supplies, we will schedule a follow-up to evaluate our solution, perform some deep cleaning and also analyze consumption to provide you the most economical dosing systems.
UP Flex Plate
BRING FLEXO PRINTING TO THE NEXT LEVEL
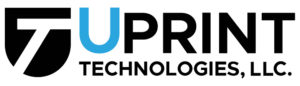

The delicate balance between equipment and consumable
No one else than you knows better that high quality flexo printing requires from you managing the delicate balance between the right equipment and using the right consumables. Therefore, to support you in achieving your high printing quality objectives, UPrint Technologies has developed an aligned solutions concept for better flexo printing:
UP Flex Plate Application
UP-Flex Plate, powered by UPrint Technologies, is an elastomer printing material for that reason developed for use in flexo printing. That is why its typically applications are found in flexible packaging, labels and also in tissue printing.
Additionally combined with the direct laser engraving solution, you will create a standardized flexo plate making process, with guaranteed reproducibility.

More benefits of this plate are that you will realize:
- sharp as well as crisp printed letter type
- both sharp as well as crisp printed ® and © mark
- hence perfect registration
- above all excellent color management
UP-Flex Plate offers longevity in printing, optimum ink transfer as well as high print quality and is solvent resistant. Besides a sheet UP-Flex Plate is also available on a roll. UP-Flex Plate is to this end aligned with direct laser technology, with an unrivaled resolution of 5,080 dpi.
A one of a kind industrialized Flexo Plate making process consisting of only four process steps
Once you choose for UP-Flex Plate combined with direct laser technology you also choose for a standardized four-step flexo printing plate making process:
Step 1.
As a first step the UP-Flex Plate is mounted onto the print sleeve or cylinder. Since you can engrave the plate directly on sleeve or cylinder, precise mounting of the UP-Flex Plate is not needed.

Step 2.
During the next step engraving is done in register when using direct laser solution. The plate is immediately fit to register (no further registration is needed).

Step 3.
Following engraving of the plate, you only need to rinse the plate with water. Because a filter will out coarse particles, residual water is harmless

Step 4.
Finally the plate is ready to print. UP-Flex Plate is reusable, storable and can also be disposed eco-friendly (considered normal household waste).

A competitive edge
Finally you have an alternative to offer your customers a competitive edge in displaying their outstanding state of the art packaging, with the highest print quality at high production efficiency, short time to press and at the lowest price.
For the purpose of cleaning your UP Flex Plate, UPrint recommends using a dedicated FlexoClean Flexo Plate Cleaning cleanser to achieve the best cleaning results without abrasing your plate or sleeve.
Technical Data
Material | EPDM / Elastomer Black |
Shore A | 65 Shore A / 80 Shore A |
Compressibility | 1.14 mm (135 N/cm2 >_ 0.03mm)* |
Back | 0.007″ Polyester |
Plate Thickness | 0.045″ – 0.250″ |
Maximum width of plate | 50″ |
Maximum length of roll | 9.5 meters |
Surfaces | Fine Grind |
Roughness | Ra : 0.9 micron |
*suitable for UV curing inks, solvent-based inks, alcohol-based inks, as well as water-based inks.