WEKO ProTec
FUNCTIONAL TEXTILE FINISHING
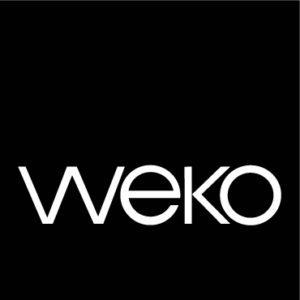

WEKO | ProTec
Create a Clean and Safe Working Environment
WEKO | ProTec is an enclosed Application System with extraction capabilities, and thus especially designed for critical chemicals to ensure a clean working environment. Applications range from the Nonwovens Industry to Textiles, Plastic Film and Tissue. Liquid finishes include for instance Antimicrobials, Hydrophobic/Hydrophilic, Softeners, Flame Retardant, Silicones, Oily Lubricants, Resins and many more…
The WEKO | Protec in brief
The fluid is evenly distributed over the web through fast spinning rotor discs by centrifugal forces. Therefore, a uniform film of ultra-fine droplets is created. The WEKO | ProTec consists of two enclosed units, each with a dedicated suction pipe on top and bottom.
This solution has two enclosed elements. Either a rotor carrier unit and a catch unit on the opposite side or with two opposite rotor carrier units working according to the principle of WEKO-Sigma. This allows for high precision, single or double sided web application. The carrier includes an automatic traversing unit to open the system for easy web insertion and high serviceability. The WEKO extraction cabinet has an adjustable extraction volume as well as an exhaust air connection for customer-side piping.
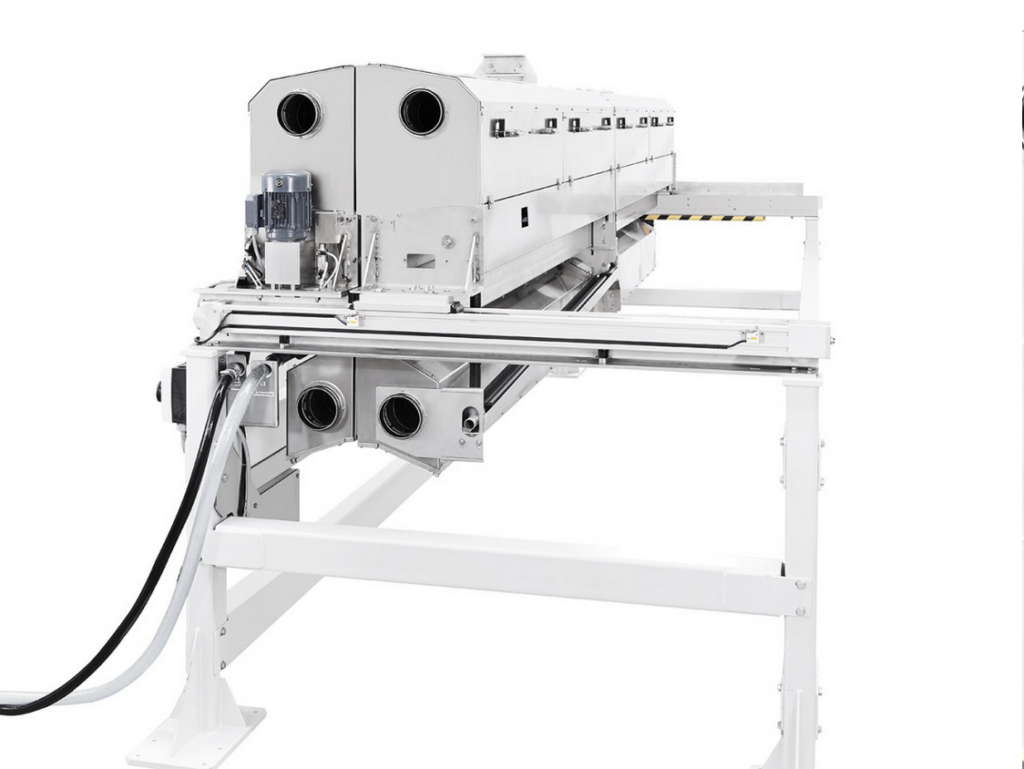
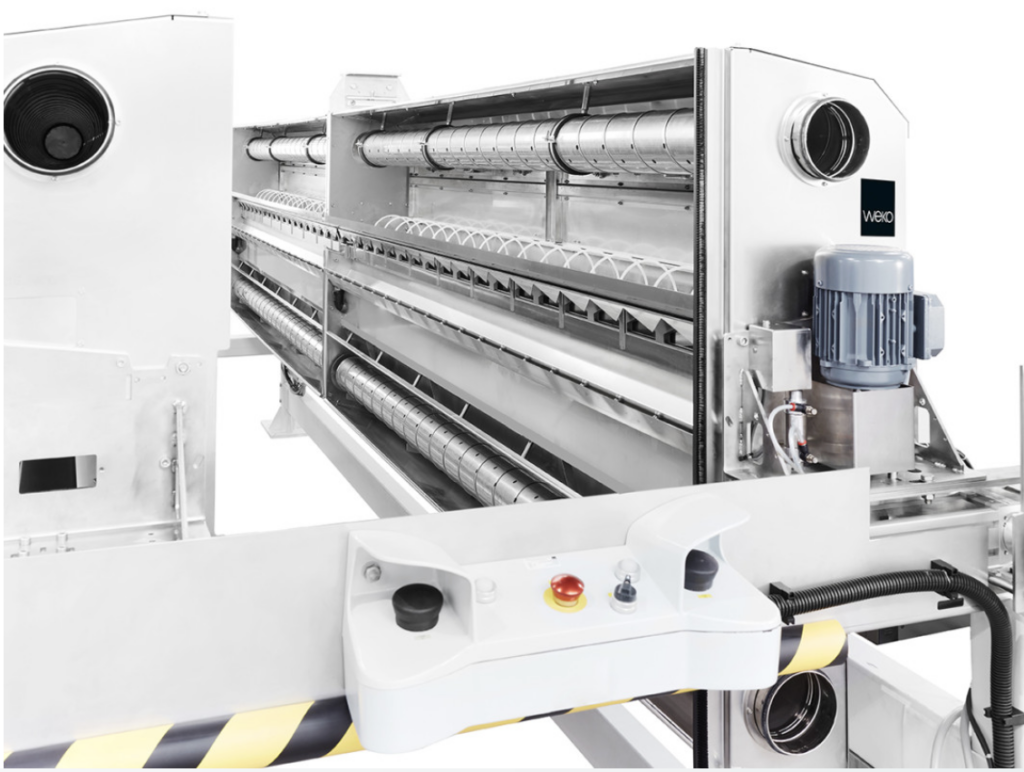
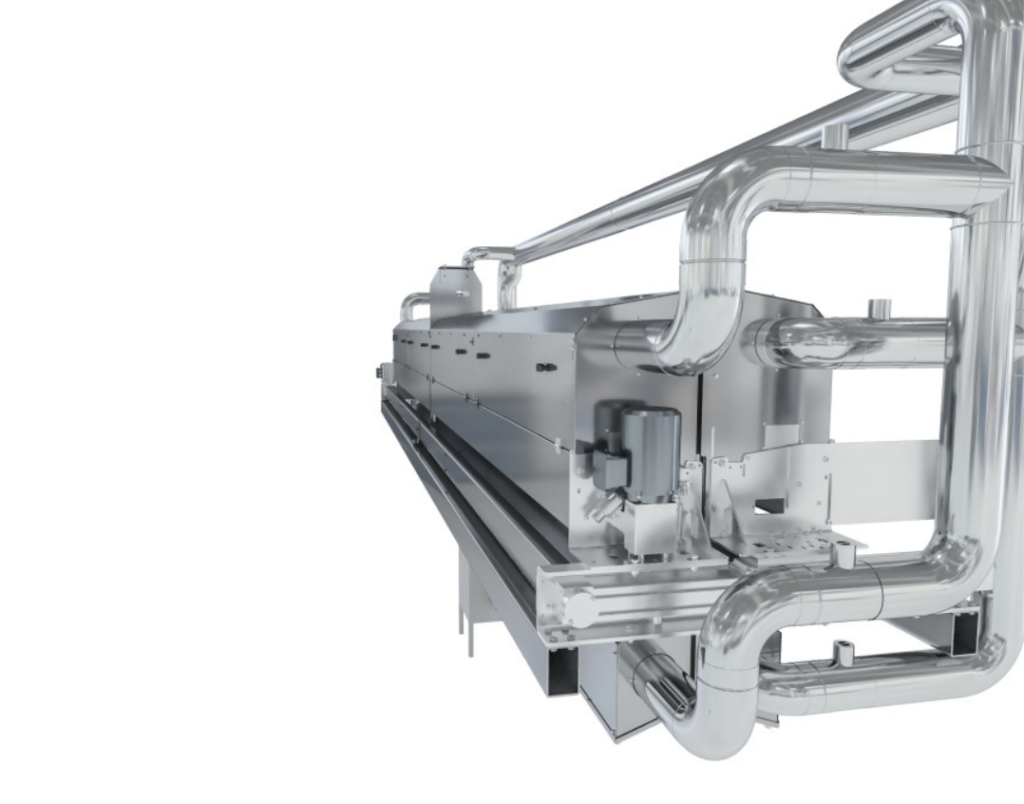
A Safe and Clean Way of Textile Finishing
Thanks to the encapsulated the functional textile finishing is safe. Undoubtedly, this solution protects significantly against escaping of aerosols. Furthermore, the special design creates a clean working environment. The building of the web is easy and fast. A highly efficient extraction unit provides the desired protection, once the unit is closed.
Your Benefits
- Contactless and precise minimum application
- Protection of the production environment and employees
- Single-sided, double-sided or different applications per side
- Fully variable format settings (option)
- Automatic speed adjustment
- Shutter system for fast start/stop/standby function
- High production speeds up to 2000 m/min.
- Working widths from 292 mm up to 7500 mm
- Low maintenance and spare parts requirements
How to start?
UPrint Technologies has a very advanced team, that will advise you about the possibilities of the WEKO technology. With your call, we will get you started and experience how the WEKO technology will improve the digital printing results. We also offer the option to run test trials or provide equipment loaners for dedicated performance test.
Download a Brochure
Product Brochure WEKO Protec |
Product Brochure WEKO Protec 2020 |
Product Brochure WEKO Protec Antimicrobial |
WEKO NEO
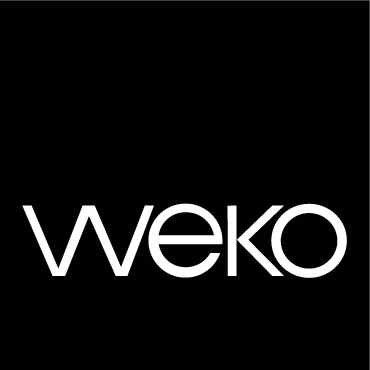
TEXTILE REVOLUTION WITH WEKO | NEO

WEKO | NEO
Textile revolution with WEKO | NEO is here. Since the world-wide textile production is suffering from cost pressure and the desire to reduce consumption of water, energy and chemicals. Therefore, the advanced WEKO | NEO technology combines a more sustainable process with cost saving production.
A newly developed innovation for the textile industry to revolutionize the wet-on-wet and wet-on-dry finishing process. For instance, immense water, energy and chemical savings will help you to a sustainable production process. What’s more, the WEKO | NEO is used for a large variety of finishing applications in the Textile World and can be also used for Yarn dying. In addition, WEKO has partnered with Chemical Manufacturers to find excellent savings and product effects in the DENIM Manufacturing.
The WEKO | NEO technology in brief – Single or both sides fluid application
The specially designed WEKO | NEO system and the new processing is adaptable to any existing or new stenter frame, coating or Pad-Steam line or on any section of a slasher or loop dyeing range. One system fits it all spending the given savings in resources and costs.
Preferred Supplier Status
Brands and retailers are massive looking for new sustainable textile processing. Be the most liked brand supplier!

WEKO | NEO
Your Benefits
- Uniform, precise and contactless minimum application
- Single-sided, double-sided or double-sided different application
- Dye bath / chemical bath remains clean
- no tailing
- No center-side variation
- Low pick-up of only 12-35
- up to 80% less drying energy
- up to 80% less fresh and waste water consumption
- up to 60% less chemical consumption
- Easy installation also on existing machines
- Easy operation via touch screen